Some keywords need to know before tube bending processes introduction. They are CLR---This is the distance from the center of curvature to the centerline (axis) of the pipe.
Outside Diameter (OD): is the distance across the extreme outside dimensions of a tube or pipe.
Inside Diameter (ID): is the longest distance across the inside dimensions of a tube or pipe.
Wall Thickness: It is the distance between the outside diameter and the inside diameter of the tube.
Degree of Bend: This relates strictly to the number of degrees required in a particular bend. |
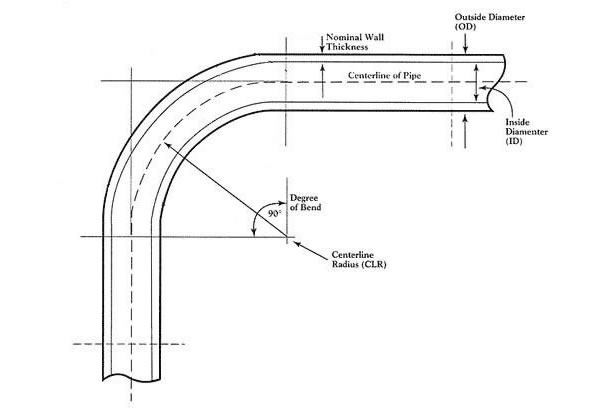 |
|
Why does the tubes need to bend ?
Tube bending is one of the most common forming processes in the field of industrial manufacture. In fact, tube bending is considered the key components of the final product or as part of a system, especially in some products within liquid flow, Such as: automobile , machinery etc.
How many types of tube bending?
In order to meet various products requirements, multiple methods of tube bending applies to different materials and sizes. In Genera, there are three approaches known respectively as compression bending, roll bending and draw bending.
|
Compression tube bending
Press bending is the simplest and cheapest method of bending tube. It is often used to bend complex components with small diameter and soft material like copper tube. Some quite elaborate shapes can be produced. The pipe or tube is often deformed into an oval shape depending on the wall thickness of the material. This process is used where a consistent cross section of the pipe is not required. |
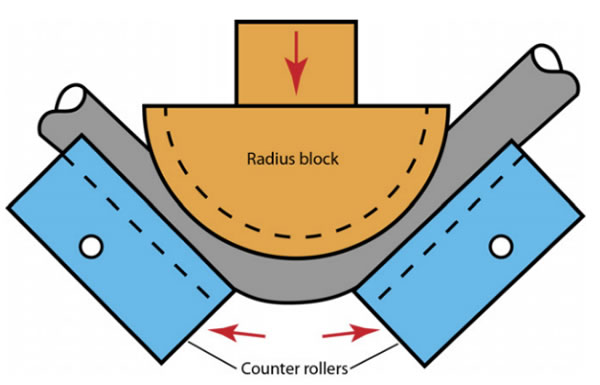 |
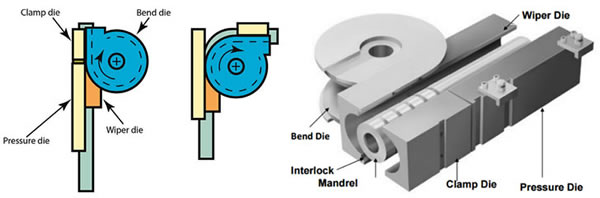 |
Draw Bending(Mandrel Bending
Draw bending is the normal forming way when we need normal bending diameters and hard materials, like carbon steel stainless steel. Draw bending overcomes some of the collapsing problems that can occur with compression bending. The materials of some tubes with thin wall is still possible to collapse during draw bending process. It requires a mandrel to insert the tube and remains inside the tube during the bend process to support the shape of wall and to avoid wall sunken happened. This is why draw bending is always referred to as mandrel bending. This is also one of key services on tube bending in MYT Technology Company . As follows, we mainly talk about the mandrel bending. |
Roll Bending
If you need a very large radius bending tube. This is where roll bending, sometimes called push bending, comes into play. For roll bending, it is a process pushing the tube through three rollers. Three rollers are at the three vertices of the triangle as figure 3 shows. The tubes from roll bending are mostly used in the field of lighting and furniture. |
|
Why does the tubes need to bend ?
Tube bending is one of the most common forming processes in the field of industrial manufacture. In fact, tube bending is considered the key components of the final product or as part of a system, especially in some products within liquid flow, Such as: automobile , machinery etc.
How many types of tube bending?
In order to meet various products requirements, multiple methods of tube bending applies to different materials and sizes. In Genera, there are three approaches known respectively as compression bending, roll bending and draw bending.
Compression tube bending
Press bending is the simplest and cheapest method of bending tube. It is often used to bend complex components with small diameter and soft material like copper tube. Some quite elaborate shapes can be produced. The pipe or tube is often deformed into an oval shape depending on the wall thickness of the material. This process is used where a consistent cross section of the pipe is not required.
Draw Bending(Mandrel Bending
Draw bending is the normal forming way when we need normal bending diameters and hard materials, like carbon steel stainless steel. Draw bending overcomes some of the collapsing problems that can occur with compression bending. The materials of some tubes with thin wall is still possible to collapse during draw bending process. It requires a mandrel to insert the tube and remains inside the tube during the bend process to support the shape of wall and to avoid wall sunken happened. This is why draw bending is always referred to as mandrel bending. This is also one of key services on tube bending in MYT Technology Company . As follows, we mainly talk about the mandrel bending.
Roll Bending
If you need a very large radius bending tube. This is where roll bending, sometimes called push bending, comes into play. For roll bending, it is a process pushing the tube through three rollers. Three rollers are at the three vertices of the triangle as figure 3 shows. The tubes from roll bending are mostly used in the field of lighting and furniture.
What effects will tube have during bending process?
1. Physical Effects on Pipe and Tube from Bending
The interior wall wrinkles and become thicker during bending process.
The exterior wall becomes stretched and thinner.
Deformation of interior and exterior wall make the tube cross section to form and reduce an oval shape.
2. Mechanical Effects on Pipe and Tube from Bending
The mechanical properties of the materials are also altered during the bending process. Yield and tensile strengths become a little bigger when tube bends. Elongation decrease somehow, because bending tube tend to collapse easily.
In general, malleability and toughness of bend tube tend to decrease. Rigidity becomes stronger.
3. Annealing and Tempering
Annealing is the treatment of a metal or alloy to reduce its brittleness and improve its ductility. Annealing is often referred to as the softening of a metal.
If a metal becomes work hardened it may require softening before work is continued, otherwise it might fracture. Annealing is achieved by the application of heat. Copper pipes are annealed before spring bending. The pipe is heated to a dull red colour and then allowed to cool or quenched in cold water.
Tempering or hardening, is a process of improving the characteristics of a metal, especially steel. Tempering is carried out by heating the metal to a high temperature and then cooling it, usually by quenching it in oil or water.
If you need a very large radius bending tube. This is where roll bending, sometimes called push bending, comes into play. For roll bending, it is a process pushing the tube through three rollers. Three rollers are at the three vertices of the triangle as figure 3 shows. The tubes from roll bending are mostly used in the field of lighting and furniture.
How to bend tube accurately?
Once you have gasped the fundamentals of how a tube is bent and are familiar with the tooling necessary to bent tube accurately, the most important thing you can do to bend accurately is set up your tooling correctly. So often the reason for common bending problems is improperly set tooling. Checking the positioning of the tooling is almost always the first step in troubleshooting any bending problem. Precise tooling setting is key to accurately bending tube.
Working experiences
Standard draw bend radius is 2 * D 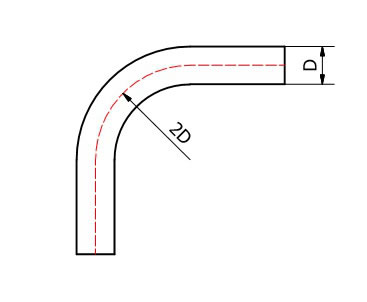
It means the minimum bend diameter mostly suggested is 2*D. For example, if you have a tube with OD 40 mm, the min CLR(bend radius) should be 80 mm. If you need tighter bend radius, even as low as ½ x D, it can be also reached though min 2*D is suggested. The bend radius is too small to collapse easily for the outside wall. It becomes very thin and require material to be with high toughness. Meantime, the inside wall go to very thick. The wrinkles are bigger and bigger as CLR tighter even like waves. In order to make the wall smoother, 1. material knowledge is necessary to have when you plan to design one bending tube; 2. Heat induction bending is suggested to use with mandrel bending at the same time. This is the working experiences from MYT Technology Company’s engineers.
Springback
The cause of springback is uneven stretching of material during a bend. The centerline material is trying to return to its original shape, yet is constrained by the unyielding material on either side. The effect is noticed when the material is taken out of the bender. Springback must be compensated for by adding the springback factor to the desired degree of bend. You can easily figure out the springback factor by performing test bends. Springback is not a constant factor for all materials and can even change within materials of the same OD and wall thickness. It's extremely important to perform test bends on each batch of material . If you want to bend a piece of tubing to 90 degrees and you determined in your test bends that the material will spring back X degrees, you must bend the tubing X degrees past 90 (9X degrees) to achieve your desired 90-degree bend when you remove the tubing from the bender.
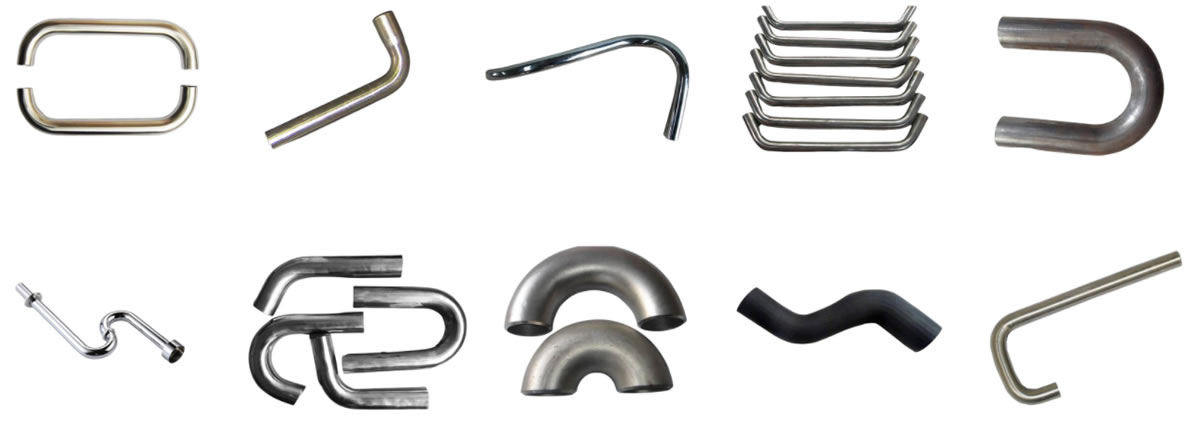
FAQ for bend tube
1. What grade of aluminum alloy tube do you recommend to bend in MYT Technology Company?
3003 series.
5052 series.
6061 series.
2. What bend tube are mostly used in bicycle?
6061 Series
3. What types of bending machines MYT have?
Mandrel Bending Machine and Induction Bending Equipment
4. What is lead time for one or several bend tube sample?
Normally, 10-15 days if mandrel bending, because die making will take some days.
5. Do MYT bend steel tubes?
Yes, various stainless steel and carbon steel tubes can be well bent in MYT.
6. Why choose us ?
Nice attitude , professional and high responsibility.
Welcome to have a nice trial order. |